Advanced Electrical Machine Design and Optimization
A special issue of Energies (ISSN 1996-1073). This special issue belongs to the section "F: Electrical Engineering".
Deadline for manuscript submissions: closed (20 February 2023) | Viewed by 27956
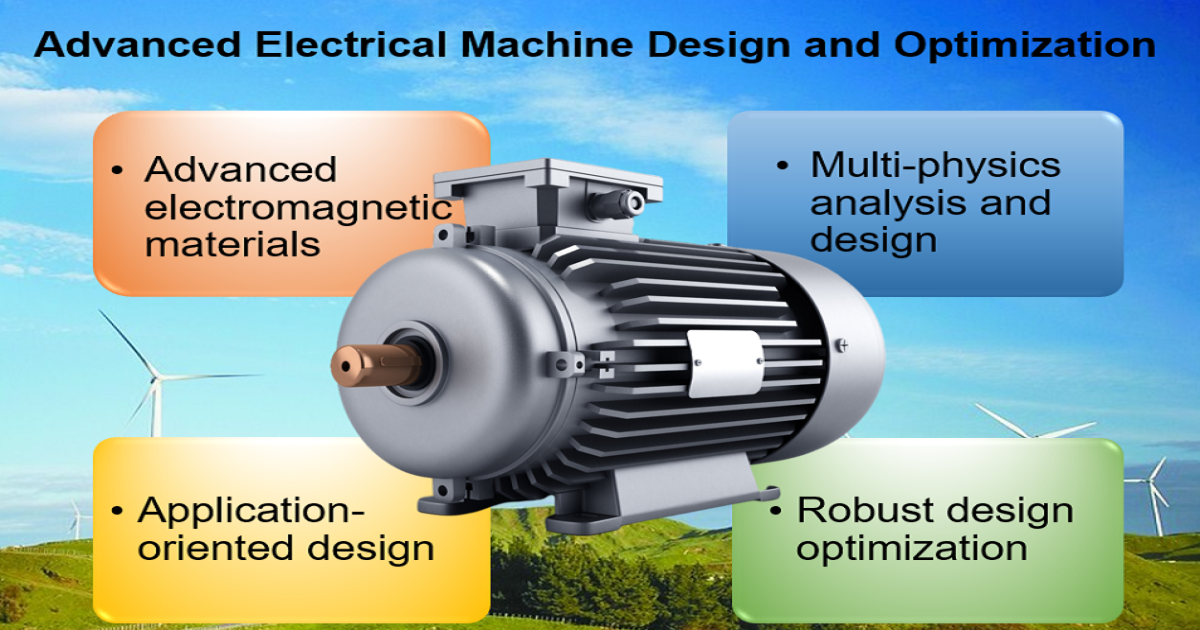
Special Issue Editors
Interests: measurement and modeling of magnetic properties of magnetic materials; electrical machine design and optimization; electric motor drives and control
Special Issues, Collections and Topics in MDPI journals
Interests: computational electromagnetics; advanced electrical machines and drive systems for electric vehicles; optimal energy management systems for microgrids and virtual power plants; multidisciplinary design optimization methods based on AI and cloud services
Special Issues, Collections and Topics in MDPI journals
Interests: computational electromagnetics; design and optimization of motor core loss; advanced electrical machines and drive systems for electric vehicles
Special Issues, Collections and Topics in MDPI journals
Special Issue Information
Dear Colleagues,
Electrical machines play crucial roles in modern industry and domestic applications. This Special Issue aims to publish recent developments on the advanced design and optimization of electrical machines, such as new design and analysis techniques, system-level, multi-objective, multi-level, multi-physics, and robust design optimization of electric drive systems.
We look forward to your recent works in this area!
Prof. Dr. Youguang Guo
Dr. Gang Lei
Dr. Xin Ba
Guest Editors
Manuscript Submission Information
Manuscripts should be submitted online at www.mdpi.com by registering and logging in to this website. Once you are registered, click here to go to the submission form. Manuscripts can be submitted until the deadline. All submissions that pass pre-check are peer-reviewed. Accepted papers will be published continuously in the journal (as soon as accepted) and will be listed together on the special issue website. Research articles, review articles as well as short communications are invited. For planned papers, a title and short abstract (about 100 words) can be sent to the Editorial Office for announcement on this website.
Submitted manuscripts should not have been published previously, nor be under consideration for publication elsewhere (except conference proceedings papers). All manuscripts are thoroughly refereed through a single-blind peer-review process. A guide for authors and other relevant information for submission of manuscripts is available on the Instructions for Authors page. Energies is an international peer-reviewed open access semimonthly journal published by MDPI.
Please visit the Instructions for Authors page before submitting a manuscript. The Article Processing Charge (APC) for publication in this open access journal is 2600 CHF (Swiss Francs). Submitted papers should be well formatted and use good English. Authors may use MDPI's English editing service prior to publication or during author revisions.
Keywords
- electrical machine
- electric motors and drives
- advanced analysis
- advanced design and optimization
- application of advanced electromagnetic materials
- multi-physics analysis and design
- robust design optimization
- application-oriented design