Mechanical Performance and Microstructural Characterization of Light Alloys (Volume II)
A special issue of Materials (ISSN 1996-1944). This special issue belongs to the section "Metals and Alloys".
Deadline for manuscript submissions: 20 June 2024 | Viewed by 2100
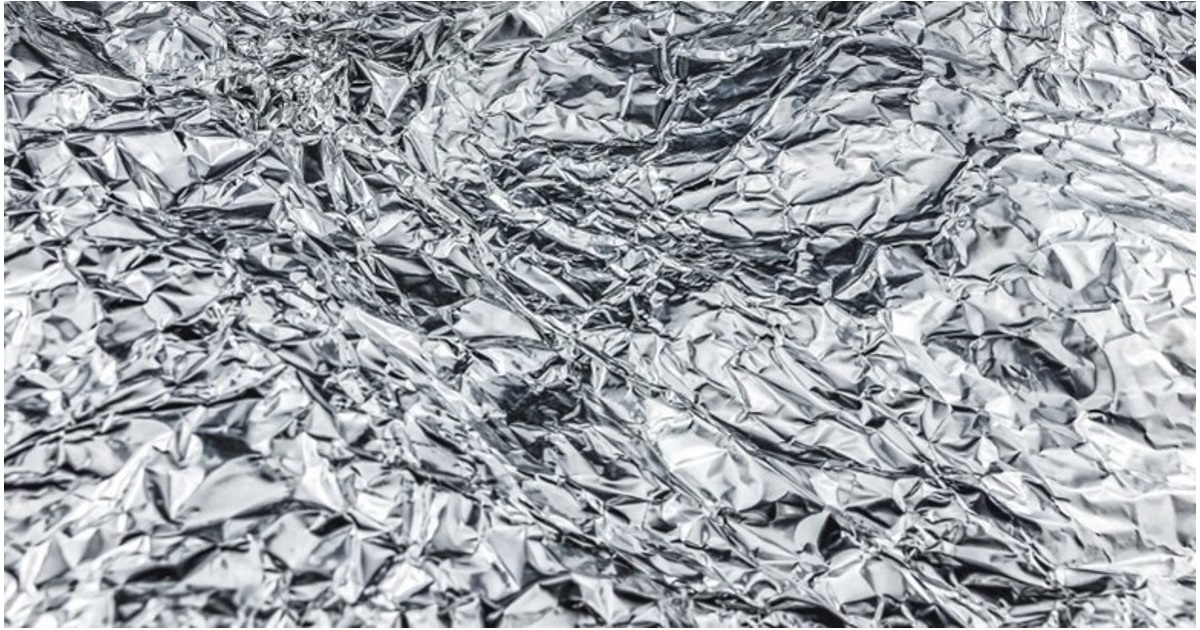
Special Issue Editor
Interests: microstructure characterization; plastic deformation and recrystallization of light metals; mechanical property
Special Issues, Collections and Topics in MDPI journals
Special Issue Information
Dear Colleagues,
After our successful first volume of the Special Issue “Mechanical Performance and Microstructural Characterization of Light Alloys”, we decided to make the special issue as a collection on light alloy. Light alloys, such as aluminum, magnesium and titanium, are important materials for the automobile, aircraft, and electronic industries. In recent decades, fruitful studies have reported on the microstructure characteristics, mechanical performance, and the advantages of light alloys. Many outstanding studies have accelerated the fast progress of our everyday life. Of course, to the best of our knowledge, there are still many unknown theories and unsolved problems in light alloys. Thus, to further trigger the development of light alloys, we should research the relationship between microstructure characteristics and mechanical performance more deeply. For this reason, the present Special Issue “Mechanical Performance and Microstructural Characterization of Light Alloys” is proposed. This Special Issue aims to collect excellent studies on light alloys from around the world, including but not limited to aluminum alloys; magnesium alloys; titanium alloy; mechanical performance; microstructure characterization; heat treatment; plastic processing; precipitation; phase transformation; SEM; EBSD; FIB; TEM; and in situ X-ray.
We welcome you to submit your excellent work to this Special Issue, “Mechanical Performance and Microstructural Characterization of Light Alloys”, which will be published in Materials.
Dr. Qinghuan Huo
Guest Editor
Manuscript Submission Information
Manuscripts should be submitted online at www.mdpi.com by registering and logging in to this website. Once you are registered, click here to go to the submission form. Manuscripts can be submitted until the deadline. All submissions that pass pre-check are peer-reviewed. Accepted papers will be published continuously in the journal (as soon as accepted) and will be listed together on the special issue website. Research articles, review articles as well as short communications are invited. For planned papers, a title and short abstract (about 100 words) can be sent to the Editorial Office for announcement on this website.
Submitted manuscripts should not have been published previously, nor be under consideration for publication elsewhere (except conference proceedings papers). All manuscripts are thoroughly refereed through a single-blind peer-review process. A guide for authors and other relevant information for submission of manuscripts is available on the Instructions for Authors page. Materials is an international peer-reviewed open access semimonthly journal published by MDPI.
Please visit the Instructions for Authors page before submitting a manuscript. The Article Processing Charge (APC) for publication in this open access journal is 2600 CHF (Swiss Francs). Submitted papers should be well formatted and use good English. Authors may use MDPI's English editing service prior to publication or during author revisions.
Keywords
- aluminum alloys
- magnesium alloys
- titanium alloy
- mechanical performance
- microstructure characterization
- heat treatment
- plastic processing
- precipitation
- phase transformation