High Speed Air Compressor for a Fuel Cell System for Use in a Vehicle
A special issue of Machines (ISSN 2075-1702). This special issue belongs to the section "Vehicle Engineering".
Deadline for manuscript submissions: closed (15 August 2022) | Viewed by 20932
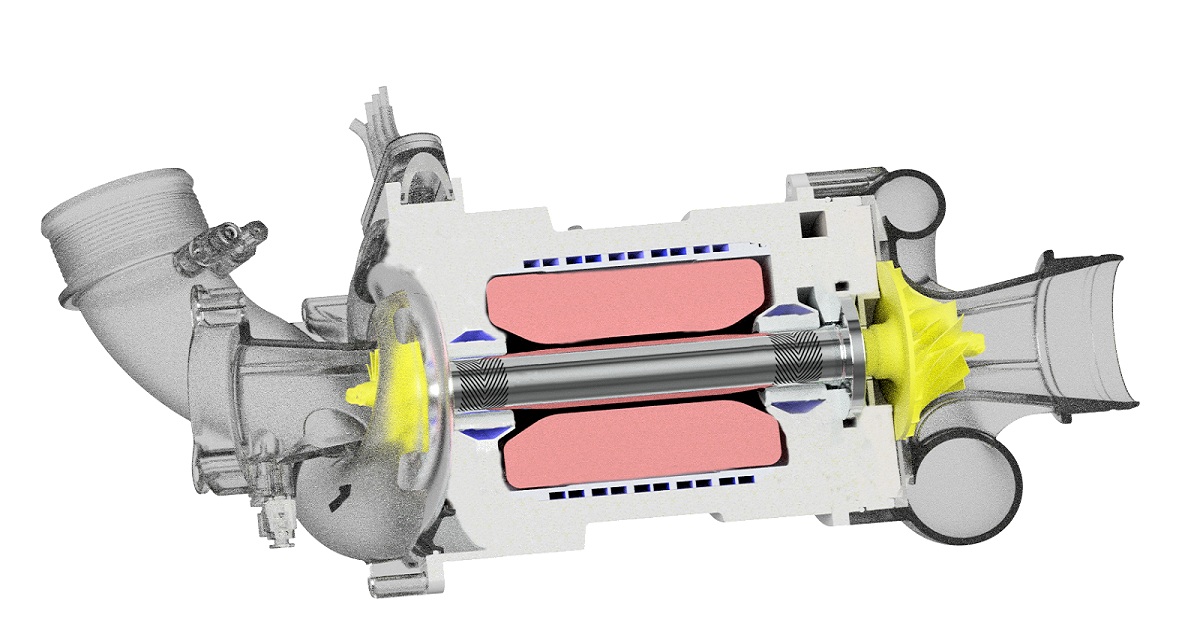
Special Issue Editors
Interests: structural dynamics: experimental system identification, tribology, vibration measurement, mechanical testing
Interests: fibre composites (dual matrix composites; nanocomposites; hybrid materials); light weight structures (CFRP airframes; innovative high lift systems); smart materials (carbon nanotube actuators; adaptive composites); adaptive structures (active structural acoustic control; aktive shape control; adaptive vibration reduction); structural dynamics (experimental system identification; structural nonlinearities)
Special Issues, Collections and Topics in MDPI journals
Interests: fibre composites; dual matrix composites; numerical simulation; computational fluid dynamics; finite element analysis; mechanical properties; mechanical behavior of materials, mechanical testing; finite element modeling; mechanics of materials; material characterization
Special Issue Information
Dear Colleagues,
In order to lower the human contribution to climate change, the reduction of CO2 emissions is a global concern. New drive concepts such as battery electric cars have a high potential to lower the carbon foot print of personal mobility. Other approaches such as fuel cell cars are usually neglected due to their comparatively poor efficiency. However, they have great advantages in terms of ranges and refueling time. An important component of fuel cell drives with high potential for savings and optimization is the electric air compressor.
This research project is, therefore, concerned with the design and further development of an electrically driven air compressor, aiming at a technology readiness level of 8. In addition to increasing the efficiency by optimizing spiral groove bearings, air flow and temperature management, the goal is also to reduce costs. Therefore, material selection and simplification of production and assembly are of particular concern.
This Special Issue covers the following main topics in particular:
- Shaft bearing and materials;
- Aerodynamics and map extending and stabilizing measures;
- Power electronics for controlling the air compressor control;
- Overall engine design and construction of test vehicles;
- Component testing;
- Manufacturing concept.
Dr. Naser Natsheh Al
Prof. Dr. Michael Sinapius
Prof. Dr. Christian Hühne
Guest Editors
Manuscript Submission Information
Manuscripts should be submitted online at www.mdpi.com by registering and logging in to this website. Once you are registered, click here to go to the submission form. Manuscripts can be submitted until the deadline. All submissions that pass pre-check are peer-reviewed. Accepted papers will be published continuously in the journal (as soon as accepted) and will be listed together on the special issue website. Research articles, review articles as well as short communications are invited. For planned papers, a title and short abstract (about 100 words) can be sent to the Editorial Office for announcement on this website.
Submitted manuscripts should not have been published previously, nor be under consideration for publication elsewhere (except conference proceedings papers). All manuscripts are thoroughly refereed through a single-blind peer-review process. A guide for authors and other relevant information for submission of manuscripts is available on the Instructions for Authors page. Machines is an international peer-reviewed open access monthly journal published by MDPI.
Please visit the Instructions for Authors page before submitting a manuscript. The Article Processing Charge (APC) for publication in this open access journal is 2400 CHF (Swiss Francs). Submitted papers should be well formatted and use good English. Authors may use MDPI's English editing service prior to publication or during author revisions.
Keywords
- air compressor
- aerodynamic bearing
- fuel cell
- spiral grove bearing
- temperature management
- component testing
- manufacturing concept